Turbines are pivotal in sustainable energy’s growth, symbolizing renewable energy progress. Renewable energy’s low environmental impact relies on merging power plant safety with stringent turbine protocols. Power plant turbine maintenance is critical for efficiency and safety. Maintaining turbine safety is essential for a power plant’s integrity.
Operators focus on enhancing turbine safety measures. Adhering to safety guidelines is not just about compliance; it’s a fundamental ethical duty. This commitment helps ensure the reliability of power for communities relying on renewable energy.
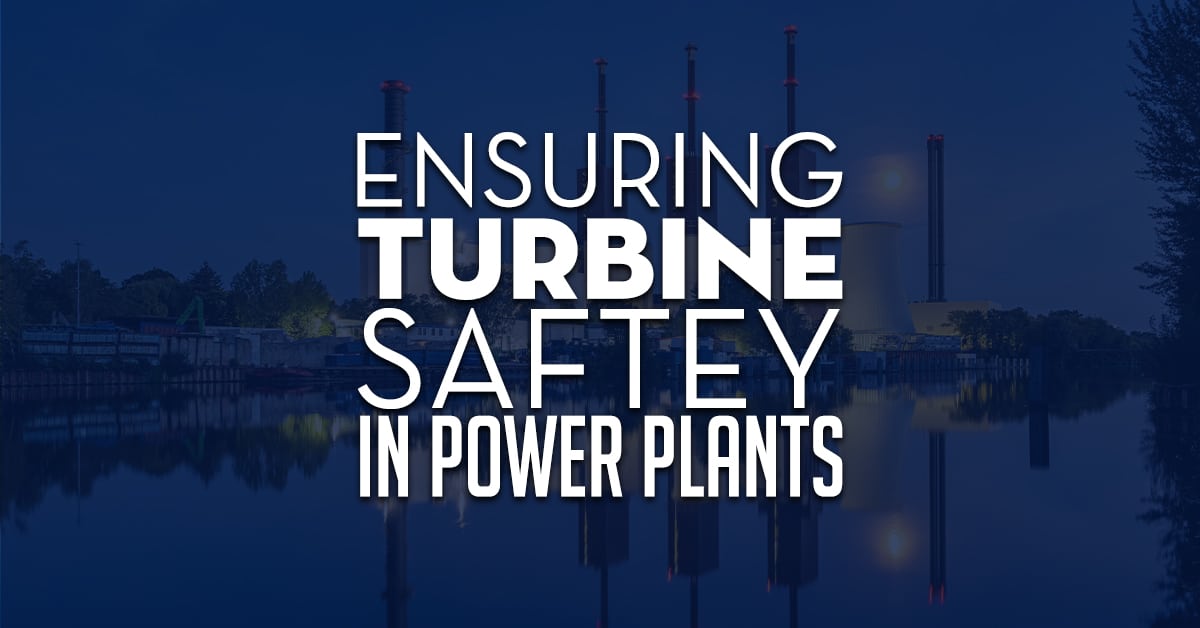
Key Takeaways
- Robust turbine safety protocols are critical for the sustainable function of energy production.
- Regular power plant turbine maintenance is essential for worker safety and operational efficiency.
- Quality power plant safety standards ensure compliance and enhance the reputation of the energy sector.
- Turbine operation demands consistent managerial oversight and proactive safety measures.
- Employing effective turbine inspection procedures minimizes risk and reinforces plant sustainability.
- Energy providers must ensure plant safety to protect both employees and the wider community.
Understanding the Importance of Turbine Safety in the Energy Sector
Technology in energy production has made turbines essential in power generation. They harness energy from wind, water, and natural gases, making turbine safety measures vital. These elements not only boost energy output but also protect the environment and human health. Ensuring safety is key for a sustainable, resilient energy sector.
The Role of Turbines in Modern Energy Production
Turbines are core to clean and efficient energy production processes. They convert kinetic energy into usable power, being crucial in the industry. Yet, the responsibility necessitates strict turbine risk assessment practices. These assessments identify hazards, ensuring gas and steam turbines operate smoothly in a demanding energy landscape.
Historical Perspective on Turbine Safeguards
Looking back, turbines have significantly evolved, especially in safety features. From simple to advanced machinery, this evolution offers more efficient and safer turbines. Advanced safety measures are now standard, showing the industry’s focus on risk mitigation and personnel and environmental protection.
Statutory Compliance and Regulatory Framework for Power Plant Safety
Turbine operation is tightly regulated to ensure safety. Environmental regulations address today’s eco-conscious demands, promoting minimal ecological impact and safety compliance. Power plants must follow these protocols, fostering a balance between energy production and environmental care. The American Clean Power Association advocates for best practices, guiding safer turbine use across the sector.
Safety measures, risk assessment, and environmental regulation compliance uphold turbine integrity in power generation. Proactive strategies, innovation, and a commitment to compliance maintain the safety and efficiency of energy sector turbines.
Ensuring Turbine Safety in Power Plants
A robust power generation facility prioritizes safety, especially within the complex realm of turbine machinery. Operators manage seamless turbine functionality while upholding turbine inspection procedures. These practices act as the first defense against machinery malfunctions. They elevate power plant equipment safety to a top concern.
The industry’s proactive hazard prevention is shown through safety systems and alarm systems. Real-time detection allows for quick intervention, which is key in identifying risks early. These measures enable fast actions during turbine operation. Furthermore, protective equipment is essential for the safety of those who work with these powerful machines.
In the realm of safety tech, the significance of safety sensors is paramount. Companies like SICK set the standard with top-notch sensors. These tools monitor rotor blades, positioning, and rotor lock systems. Their role is critical in ensuring the turbine’s integrity and the maintenance team’s safety.
Protective Measure | Application | Benefit |
---|---|---|
Alarm Systems | Malfunction alerts | Immediate notification of potential faults |
Safety Systems | Operational safeguards | Enhanced control over turbine functionality |
Protective Equipment | Personnel safety | Reduction of injury risk to workers |
Real-time Detection | Monitoring of anomalies | Swift response and continuous supervision |
The field of energy production combines advanced technology, vigilance, and strict procedures. This blend ensures turbine safety is not just a concept but an everyday reality. It protects against unpredicted events, reinforcing power plant resilience.
Comprehensive Maintenance Regimes for Turbine Longevity
With the global drive towards renewable energy, the need for rigorous maintenance regimes for turbines is more crucial than ever. Integrating valve and pump maintenance into both preventative and predictive strategies is key. This ensures the system’s resilience and longevity.
Preventative Vs. Predictive Maintenance Strategies
The balance between preventative and predictive maintenance strategies is vital for reducing downtime and maximizing efficiency. Preventative maintenance involves regular scheduled services. Predictive maintenance, on the other hand, leverages advances in technology to foresee and rectify potential problems before they arise.
Professional Training and Certification for Maintenance Staff
Empowering maintenance staff through project management and professional development is crucial. Continuing education and specialized training keep technicians adept in modern maintenance techniques. This is indispensable for ensuring turbine systems run efficiently and last longer.
Common Maintenance Challenges and Solutions in Turbine Operation
The challenge of handling degradation due to high temperatures and managing humidity requires inventive solutions. Employing control systems for precise temperature monitoring helps address these issues. It achieves a balance between efficiency and safety.
Maintenance Type | Focus | Key Components | Benefits |
---|---|---|---|
Preventative | Scheduled servicing | Valve maintenance, lubrication | Reduced unexpected failures |
Predictive | Condition monitoring | Vibration analysis, temperature monitoring | Optimized performance, reduced costs |
Innovative Safety Technologies and Procedures in Turbine Operation
The introduction of groundbreaking safety mechanisms has transformed turbine operation in power plants. Engineers and operators employ cutting-edge safety sensors that come with double-layered safety features to constantly monitor crucial turbine parts. These advanced sensors swiftly detect issues, potentially triggering an auto shutdown to prevent disasters. Adaptable across different turbine models, these technologies protect not just the machinery but also the workforce.
Another significant advancement is the utilization of wireless monitoring technologies. These innovations provide real-time data gathering and analysis, leading to better decision-making and prompt intervention. Thanks to remote monitoring capabilities, operators can manage plant safety from any location, not just the control room. This level of continuous oversight is vital for preventing severe incidents or emergency shutdowns.
Implementing these modern technologies reflects the industry’s dedication to avoiding major incidents and achieving operational superiority. Safety now involves proactive measures alongside emergency responses. Through ongoing inspections, risk evaluations, and the introduction of backup safety mechanisms, power plants are establishing new standards for secure, efficient energy production. As renewable energy sources become increasingly prevalent, these strategies will keep evolving, ensuring turbines remain key to a stable and green energy future.
Frequently Asked Questions
What are turbine safety protocols and why are they important?
Turbine safety protocols ensure power plants operate turbines safely. They protect staff, prevent damage, and maintain energy production efficiency.
How often should power plant turbines undergo maintenance?
Maintenance schedules for turbines depend on manufacturer advice, type, and operation settings. A mix of preventative and predictive strategies helps ensure longevity and safety.
What steps are taken to ensure plant safety in the context of power plant operations?
Plant safety comes from strict guidelines, risk evaluations, and safety measures. Also, thorough training, advanced systems, and adhering to safety rules are key.
How are turbine inspection procedures executed to ensure safety?
Inspection of turbines is by experts following thorough protocols. They check visually, measure performance, and examine components to find any issues.
What is the significance of turbine risk assessment in power generation?
Risk assessment for turbines is crucial for spotting hazards that could cause failures or incidents. It allows for preventive action to secure safe and efficient turbine operation.
What safety systems are integral to power plant operations?
Key safety systems in power plants include alarms, shutdown processes, fire protection, and sensor systems. These systems help prevent accidents and ensure stability.
Why are automatic shutdown systems crucial in turbines?
Automatic shutdown systems in turbines respond to failures or danger, like excess vibration or overheating. This protects operators and prevents severe damage.
In what ways do innovative safety technologies enhance turbine operation?
Innovative safety technologies boost turbine operation through better monitoring, predictive maintenance, and effective protection. Technologies such as smart sensors and wireless systems enhance safety and efficiency.