Ensuring operational excellence in power generation, gas turbine rotor balancing stands as a pivotal maintenance technique for prolonging the lifespan and enhancing the performance of turbines. In a world where energy efficiency and mechanical reliability intersect, dynamic balancing and precision are paramount. By employing specialized balancing methods in both shop and field settings, technicians work meticulously to bring rotors into the perfect symphony of motion, thereby reducing vibration and wear over time. Striving beyond the traditional balancing machine, the field leverages analytical insights to address the unique challenges of rotating machinery found in today’s complex turbine systems.
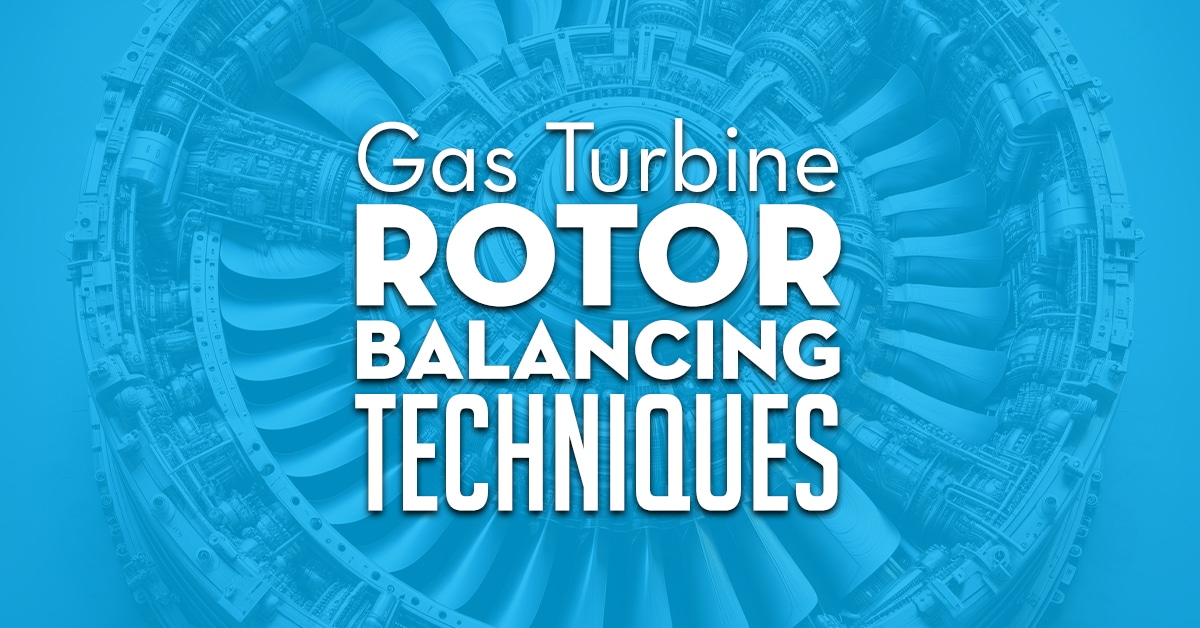
Key Takeaways
- Balancing a gas turbine rotor is critical for minimizing vibration and extending machinery lifespan.
- Dynamic balancing is a nuanced procedure that involves precise adjustments to reduce rotor imbalance.
- Techniques have evolved to cater to both flexible and long rotors, which are commonplace in modern turbines.
- Rotor balance plays a crucial role in the overall efficiency and safety of power generation equipment.
- Integrating industry standards and continuous innovation is vital to the future of rotor balancing practices.
- Advanced balancing methods, tailored diagnostics, and field testing epitomize the modern approach to tackling rotor unbalance challenges.
Understanding Rotor Unbalance and its Impacts on Gas Turbines
The reliability and efficiency of gas turbines are heavily influenced by the precision of the rotor balance process. Maintaining rotor balance is crucial for the smooth operation of turbines, but several factors can contribute to unbalance, impacting overall system performance which could lead to the need for a rotor repair.
Sources and Causes of Rotor Unbalance
Rotor unbalance occurs when there’s an uneven distribution of mass around the turbine’s rotating axis, which should be addressed promptly to avoid disruptions in gas turbine operations. The causes of unbalance can be broadly categorized into manufacturing discrepancies, such as variations in material density or faulty assembly practices, and operational causes of unbalance, which may include accumulated fouling or degradation from long-term use. This unbalance during operation can lead to the rotor becoming misaligned within its bearings or developing a bow due to uneven heating or material deposition.
Understanding these causes is imperative as they underline the necessity of a comprehensive rotor balance process. Regular monitoring and maintenance schedules can identify potential unbalance issues before they escalate into serious problems.
Consequences of Unbalance on Gas Turbine Performance
An unbalanced rotor can have far-reaching consequences on gas turbine performance. The imbalance generates centrifugal forces during rotation that causes vibration at the frequency of rotation (1xRPM), which if left unchecked, can progressively worsen to cause mechanical stress, bearing issues, and lead to costly repairs or downtime.
The impact on gas turbines ranges from reduced operational efficiency to potential damage to other components of the turbine system. Balancing not only extends the lifespan of the turbines but also ensures that they operate at peak performance levels, with minimal vibration levels and reduced wear on turbine components.
Strategies to correct rotor unbalance are complex and vary depending on the specific type of unbalance and the operational conditions under which the turbine operates. Nonetheless, it is vital to recognize the detrimental effects of neglecting the rotor balance process and to prioritize precision balance throughout the lifecycle of a turbine.
Advancements in Rotor Balancing Methods
The relentless pursuit of precision in rotor dynamics has fueled significant advancements in rotor balancing, with the groundwork laid by pioneering methods emerging as far back as the early 1930s. This relentless quest has been a response to the shifting paradigms in rotating machinery, where the demand for higher speeds and the accommodation of heavier loads is incessant. Today, the adept interplay of refined balancing techniques ensures that each rotation of a turbine blade cleaves through the air with a minimum vibration signature, underscoring the industry’s drive towards perfection.
The Evolution of Balancing Techniques
From rudimentary beginnings, balancing rotors has transitioned through an evolutionary pipeline that has continuously integrated more sophisticated technologies and computing power. The traditional Influence Coefficient Method (ICM) and Modal Balancing Method (MBM), though revolutionary at their inception, have now become part of a larger compendium of knowledge that supports the modern balance technique. These approaches have been pivotal in steering the course towards enhanced rotor stability across a spectrum of operational scenarios.
Comparing Traditional and Modern Balancing Approaches
When we juxtapose traditional balancing methods against modern balancing approaches, it’s clear there’s a stark transformation in both precision and applicability. Traditional methods laid a crucial foundation but often fell short in addressing the complexities of high-speed, flexible rotor systems, such as those found in aeronautics and energy generation equipment.
Modern methods, however, embrace a broader scope, targeting vibrations through incremental adjustments and often involve real-time surveillance of rotor dynamics. This granularity of control harmonizes the rotor’s functionality with the high-stress environments in which it operates.
Factors | Traditional Methods | Modern Methods |
---|---|---|
Scope of Application | Limited to rigid rotors | Applies to flexible and high-speed rotors |
Technological Integration | Minimal technology integration | Advanced diagnostics and computational modeling |
Adaptability | Manually-intensive; limited adaptability | Dynamic adaptability to operational changes |
Precision | Low to medium precision | High precision balancing with refined margins of error |
Operational Efficiency | Relies on extended downtime for balance checks | Permits in-situ balancing, minimizing downtime |
The evolution of balancing techniques reflects a narrative of technological triumph, one where the ingenuity of the past blends seamlessly with the digital prowess of the present. As we continue to witness the modern balancing approaches refine what we thought was already precise, it is evident that the mission to achieve near-perfect balance in rotors will propel the industry further into a future where vibration is nothing but a ghost of the past.
Principles of Rotor Balancing
The core tenet of principles of rotor balancing dictates that a rotor must have its mass center precisely aligned with its axis of rotation. This crucial alignment mitigates the inertial forces that occur during rotation, ensuring efficient vibration control and force reduction. Balancing a rotor is not about achieving perfect balance; rather, it is about reaching a state where vibration levels stay within the acceptable range for operational integrity and performance.
Dynamic balancing method are integral for maintaining harmony in rotor systems. These methods utilize influence coefficients, balance speeds, and multiple balance planes to achieve refined balance. Each implemented correction, theoretically and practically, aims to methodically minimize residual vibration. Notably, this process incorporates a variety of measurement points to accurately detect any imbalance.
- Redistribution of Mass: This involves adding or subtracting mass in calculated locations.
- Application of Balancing Weights: Precision weights are attached to strategically alter the mass distribution.
- Influence Coefficients: Data-driven calculations help target the right correction points.
- Balance Speeds: Determining the optimal speeds at which balancing should be performed.
- Multiple Balance Planes: Engaging different rotor planes to manage complex vibrational behaviors.
- Measurement Points: Selecting precise locations on the rotor for accurate imbalance detection.
This methodology, particularly the use of the dynamic balancing method, caters to the intricate requirements of both rigid and flexible rotors. Through these sustained efforts, practitioners work to guarantee the smooth operation of rotor machinery, ultimately contributing to the increased lifespan and efficiency of such systems.
Rotor Balancing in the Manufacturing Process
The integration of rotor balancing within the manufacturing process is a critical step for ensuring the long-term performance and reliability of gas turbines. By implementing initial balancing and precision techniques during assembly, manufacturers can secure an optimal balance condition that stands up to the rigors of operation.
Importance of Initial Balancing
At the forefront of rotor manufacturing lies the initial balancing phase, which establishes the foundational balance condition for the rotor. This crucial step in manufacturing not only sets the stage for a rotor’s operational stability but also significantly reduces the need for future balance correction. It is the initial act of verification against imbalance that safeguards the assembled rotor from premature wear and vibration-induced damage.
Techniques for Balancing During Assembly
Balancing during assembly is a meticulous process, demanding precise techniques to ensure that each component contributes to the overall balance of the assembled rotor. Traditional methods, such as fitting keyways and verifying the concentricity of mounting hardware, merge with modern practices like the incremental addition of components and the use of precision mandrels. These strategies are pivotal in curtailing balance errors that could compromise the rotor’s performance upon installation in gas turbines.
- Utilize half keys to ensure keyway fittings contribute to balance consistency.
- Ensure mounting hardware concentricity to prevent offsets in balance.
- Adopt precise mandrels for accurate component balancing and assembly.
- Incrementally mount components, rather than in bulk, to enhance balance accuracy.
By adhering to these balancing disciplines during the rotor manufacturing process, manufacturers can deliver a product that embodies robustness, efficiency, and a prolonged service life within the demanding environment of gas turbine applications.
Field Balancing: Addressing In-Situ Unbalance
In the world of rotor dynamics, in-situ unbalance presents a complex challenge that must be met head-on with precision and innovation. The inherent fluctuations in operational conditions and the dynamic characteristics of gas turbines necessitate a robust approach to field balancing. It’s a task that requires a balance of skill, experience, and the right tools.
Innovation in Field Balancing Tools and Techniques
Field balancing tools have seen remarkable strides in their development, catering to the nuanced demands of modern rotor systems. These innovations have transformed the process of balancing, contouring to the unique requirements that vary from one rotor to another. The tools now come equipped with features that significantly simplify the identification and rectification of rotor deflection and imbalance, even under the most stringent operating conditions.
Case Histories from Difficult Field Balancing Scenarios
Reflecting on real-world applications, challenging field scenarios highlight the efficacy and necessity of these advancements. Case histories reveal situations where rotors displayed significant in-situ unbalances, necessitating on-the-spot and precise interventions. With the blend of modern technology and refined techniques, technicians have been able to restore equilibrium, enhancing the rotor dynamic behavior and overall system performance.
Challenges | Traditional Tools | Innovative Solutions |
---|---|---|
Complex Configurations | Limited Adjustability | Modular Tool Design |
Dynamic Operating Conditions | Fixed Calibration | Real-time Data Adjustments |
In-Situ Rotor Deflection | Manual Measurement | Automated Sensing Technology |
Varying Rotor Dynamics | Generic Approaches | Customizable Balancing Algorithms |
ISO Standards and API Guidance for Gas Turbine Rotor Balancing
Ensuring the correct balance of a gas turbine rotor is crucial for its performance and longevity. Adherence to recognized standards plays a pivotal role in the rotor balancing process. The international compliance benchmarks set by ISO standards and API guidance are particularly significant, providing the framework for precision and quality within the industry.
Understanding ISO 1940 and Its Implications
The ISO 1940 standard is a critical document that outlines the required balance quality of a rotor. It specifies the permissible residual specific unbalance which essentially defines the precision in which each rotor must be balanced to. The intent is to prevent excessive vibration, which is a direct result of rotor imbalance, thereby ensuring safe and efficient operation of gas turbines.
Reviewing API Standards for Rotor Unbalance Correction
API standards take a comprehensive approach by providing detailed procedures for rotor balancing, particularly highlighting the need for dynamic balancing of individual rotor components prior to assembly. These procedures as specified in standards like API 617 offer invaluable guidance on the incremental balance method for rotor, which is vital for rotor unbalance correction without invoking significant modal unbalance in high-speed contexts.
Standard | Scope | Focus Area | Implication for Balancing |
---|---|---|---|
ISO 1940 | Balance quality requirements for rotors | Permissible residual unbalance | Precise balancing to minimize vibrations |
API 617 | Axisymmetric rotor balance | Individual component balance | Incremental balancing to prevent modal unbalance |
API 684 | API Standard for rotordynamics | Analysis of rotor dynamic behavior | Criteria for assessing and correcting unbalance |
These established ISO and API standards serve as a fundamental method for ensuring the integrity and performance of gas turbine rotors. By meticulously complying with both ISO 1940 and API guidance, industry professionals can effectively manage both rotor imbalance and rotor unbalance correction, thereby maintaining the essential balance that is characteristic of a high-performing gas turbine rotor.
Addressing the Challenges of Flexible Rotor Balancing
In the arena of high-performance machinery, flexible rotor balancing is a critical undertaking that ensures the smooth operation and longevity of rotating equipment. The complexity of flexible rotors arises from their need to operate across a range of speeds without succumbing to destructive vibrations. This calls for a comprehensive approach to understanding and overcoming rotor unbalance, utilizing advanced techniques like modal balancing and multi-plane balancing.
Modal Balancing of Flexible Rotors
Modal balancing stands at the forefront of methods used to correct multidimensional unbalance in flexible rotors. This technique considers the mode shapes of the rotor, allowing for targeted adjustments that accommodate multiple vibration modes that can occur during different operational scenarios. By employing modal balancing, technicians can achieve precision that generic balancing techniques might not offer.
- Precision placement of balancing weights
- Identification of critical speed ranges
- Adjustments accounting for different mode shapes
Case Studies: Overcoming Flexible Rotor Unbalance
Real-world applications shed light on the intricacies of balancing complex rotor systems. Case studies involving flexible rotors often highlight the necessity for detailed diagnostic processes, pinpointing the exact location and magnitude of imbalances. With a judicious combination of expertise and technology, specialists can correct imbalances that significantly affect rotor performance.
“Ensuring the proper balance of a flexible rotor not only enhances its efficiency and operational lifespan but also substantively contributes to the safety and reliability of the entire machinery system.”
Challenge | Diagnostic Measure | Corrective Action |
---|---|---|
Imbalance at High Operational Speeds | High-speed modal testing | Application of precision balancing weights |
Multiple Mode Vibrations | Operational deflection shape analysis | Multi-plane balancing correction |
Residual Unbalance Post-Assembly | Laser shaft alignment | Iterative adjustments to rotor components |
Conclusion
The realm of gas turbine rotor balancing is one characterized by its constant evolution and technical precision. Methods aimed at reducing rotor imbalance have become increasingly sophisticated, underscoring the significance of achieving a well-balanced rotor. The meticulous application of initial balancing procedures is as crucial as the advanced strategies employed for field and modal balancing. These collectively contribute to the enhanced performance and extended service life of gas turbines.
Industry practitioners recognize high-speed balancing and precision balancing as essential contributors to maintaining the integrity of a rotor assembly. Employing these techniques efficiently controls vibration amplitude, thereby ensuring stability and reliability in operation. Moreover, the integral role of gas turbines in power generation and petrochemical applications necessitates strict adherence to a comprehensive set of balancing standards to guarantee that equilibrium is maintained across varying conditions.
As we look to the future, it’s clear that the ongoing refinement of tools and methods for balancing a rotor assembly will be imperative. Only through continuous innovation and adherence to robust quality standards can we assure the performance and durability demanded by the highly specialized field of gas turbine rotor balancing. The industry’s commitment to minimizing any risks associated with rotor imbalance is one of the many testimonies to the relentless pursuit of excellence in this sector.
Frequently Asked Questions
What is rotor balancing in the context of gas turbines?
Rotor balancing for gas turbines is a precision process that ensures the mass distribution of the turbine rotor is even around its rotation axis. This reduces vibrations, promotes smoother operation, and extends the lifespan of the turbine.
What are the main causes and sources of rotor unbalance?
Causes of rotor unbalance include manufacturing discrepancies, damage during operation, changes in the balance condition, fouling from dirt, and uneven heating that can lead to rotor bowing.
What are the consequences of rotor unbalance on gas turbine performance?
Unbalance can result in excessive vibration, premature bearing wear, increased mechanical stress, reduced efficiency, and the potential for catastrophic failure of the gas turbine.
How have rotor balancing methods evolved over time?
Balancing methods have developed from basic static and dynamic balancing to advanced techniques such as the Influence Coefficient Method (ICM) and Modal Balancing Method (MBM), accommodating the complexities of modern, high-speed, and flexible rotors.
What distinguishes modern balancing approaches from traditional methods?
Modern balancing methods incorporate precision measurements, high-speed balancing, and the application of advanced algorithms, focusing on the unique dynamic characteristics of each rotor whereas traditional methods were more generalized and often incapable of addressing the intricacies of flexible rotor systems.
Why is initial balancing during the manufacturing process important?
Initial balancing ensures that each rotor component is within acceptable balance parameters before assembly, preventing imbalance that could result in poor performance and failure when the turbine is operational.
What techniques are employed during rotor assembly to ensure balance?
Techniques to ensure balance during assembly include precision fitting of keyways, ensuring concentricity of mounting hardware, and incremental addition of components to the rotor assembly.
How do field balancing tools and techniques address in-situ unbalance?
Field balancing tools and techniques employ portable balancing equipment and advanced vibration analysis to precisely identify and correct unbalance in an operational setting without dismantling the rotor or machine.
What are the implications of ISO Standard 1940 for rotor balancing?
ISO Standard 1940 defines permissible residual specific unbalance limits, balance quality grades, and provides a foundational approach to achieving precision in rotor balancing.
Why are API standards important for rotor unbalance correction?
API standards such as API 617 specify requirements for balancing individual rotor components and the assembled rotor, ensuring high-quality and reliable operation in line with industry best practices.
What is modal balancing and why is it important for flexible rotors?
Modal balancing is a technique specifically designed for flexible rotors that involves applying correction masses in multiple planes to minimize vibrations across various modal frequencies, providing stability over the operational speed range.
Can you provide examples of overcoming flexible rotor unbalance?
Case studies on flexible rotor unbalance highlight the use of modal balancing, high-speed balancing tests, and detailed vibration analysis to successfully remedy complex imbalance issues and prevent excessive vibrations.