For industries relying heavily on steam turbines, the meticulous planning and scheduling of steam turbine maintenance are paramount. This eagle-eyed foresight is a critical cog in the machinery of productivity, efficiency, and regulatory adherence. Companies like GE have honed this process to an art, crafting in-depth maintenance schedules and repair strategies that equip operators with the capability to diminish downtime and strategically schedule outages.
Enlisting a steam turbine maintenance planner to design and implement an advanced inspection program can push routine maintenance timelines further, transitioning the customary outage cycle from a rigid five to a more lenient seven years. This shift is not just about extending periods between maintenance but fostering a more reliable and efficient operation through constant monitoring and preventative service.
Maintenance and repair plans differ across the board, defined by the necessity for unique, customized solutions that not only rejuvenate existing equipment but also place industrial operations at the forefront of competitiveness. For instance, embracing something like Allied Power Group’s Component Repair program serves multiple objectives, including fostering long-term partnerships and enhancing ongoing plant performance.
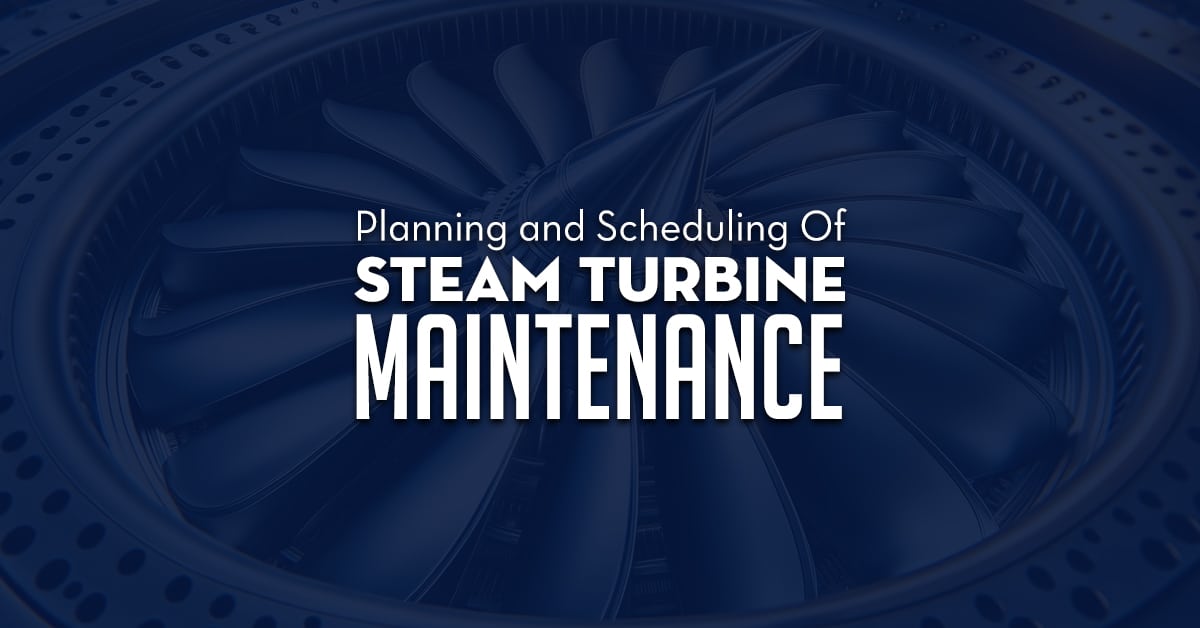
Indeed, considering the reliability and operation of steam turbines, the consensus rings clear: it begins with a thorough initial inspection and evolves into a tailor-fitted maintenance paradigm, one that recognizes the irreplaceable worth of external insight when facing the intricacies of turbine reliability, strategy, and focused risk-based analysis for comprehensive outage planning.
Key Takeaways
- Strategic steam turbine maintenance schedule minimizes downtime, enhancing productivity.
- Inspection programs like Allied Power Group’s Component Repair Program extend maintenance cycles for operations, improving long-term efficiency.
- Targeted strategies like effective scheduling for steam turbine maintenance are tailored to plant-specific requirements.
- Optimizing steam turbine maintenance planning involves constant monitoring for predictable and reliable service.
- Customized maintenance solutions modernize equipment, giving industries a competitive edge.
- The right maintenance and repair strategies lead to a proactive rather than reactive approach to turbine management.
The Importance of Regular Steam Turbine Maintenance
Maintaining the optimum condition of steam turbines is not just a matter of necessity but one of strategic importance. Regular checks and maintenance ensure that turbine components operate reliably and continue to function within their designated parameters, staving off any potential failures that might lead to unplanned operational downtime.
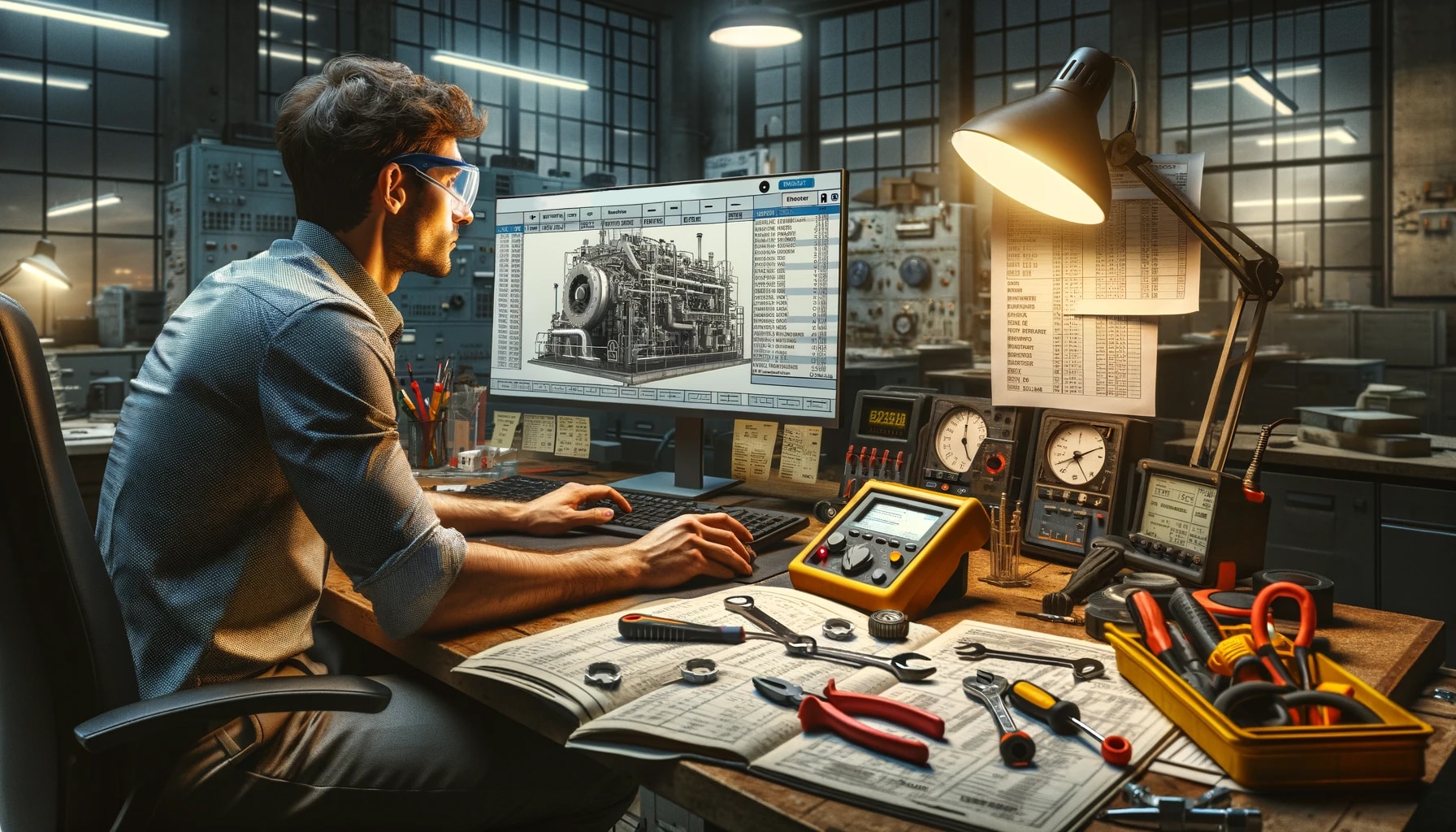
Periodic evaluations and regular inspections form the bedrock of a robust turbine maintenance strategy, one that seeks to identify and monitor potential issues before they culminate in system-wide failure. A commitment to this kind of preemptive oversight is how operators can guarantee performance reliability and the continued safety of their installations.
Understanding Wear and Aging Processes
Aging steam turbine components subjected to operational wear can jeopardize the entire turbine’s reliability. Therefore, it is crucial to monitor the onset of such wear selectively and systematically. By doing so, it is possible to predict and plan for replacement or repair, mitigating the risks associated with turbine failure.
Proactive Measures to Reduce Failure Downtime
By adopting proactive strategies, including thorough outage planning and utilizing technical services, facilities can evaluate the state of their equipment efficiently and take decisive action to circumvent extended periods of failure downtime. This approach lends itself to maintaining consistent operational standards and limiting the cost impacts of turbine failure.
Extending Equipment Life Through Maintenance
Through Reliability Centered Maintenance (RCM), a methodology that capitalizes on regular inspections and checks, it is easier to extend the service life of steam turbines. By consistently prioritizing the reliability of turbine performance, operators can ensure a long-lasting operational cycle, thereby confirming the wisdom of periodic monitoring and maintenance.
Maintenance Component | Goal | Outcome |
---|---|---|
Regular Inspections | Prevent wear through early detection | Increased reliability and performance |
Proactive Strategy | Minimize risk of unplanned down-time | Reduced operating costs and improved profitability |
RCM Approach | Analyze risks and prevent failures | Extended equipment life and modernization opportunities |
Key Steps for Effective Steam Turbine Maintenance Planning
With the objective of preserving the integrity of industrial steam turbines, it’s crucial to adopt a strategic approach towards maintenance planning. The foremost prerequisite for robust maintenance begins with meticulous scrutiny of the service providers. Recognizing high-caliber technical services, repair monitoring, quality assurance, and the overall competence of engineers becomes the bedrock of ensuring reliable and efficacious turbine operation.
Evaluating Vendor Capability and Qualification
Vendor selection is not a task to be taken lightly—performing due diligence is a cornerstone for aligning with a vendor that meets the stringent demands of turbine outage scenarios. Evaluating industrial steam turbine engineers involves a rigorous process where one assesses the mechanical expertise, tools, and procedures they possess. It’s not just about having the right equipment; it’s about ensuring quality assurance measures are enacted and adhered to throughout the repair process, under vigilant observation to align with the predefined maintenance schedule.
Developing a Customized Steam Turbine Maintenance Plan
To keep turbines spinning efficiently, a customized steam turbine maintenance plan that resonates with the unique requirements of the facility is indispensable. This plan should amalgamate proactive strategies, including the pre-ordering of parts and spotting potential opportunities for modernizing equipment. Supported by the knowledgeable insights from seasoned engineers, these tailored strategies significantly contribute to enhanced operational reliability.
Timing and Scheduling Repairs to Minimize Downtime
Engineers and facility managers must enact a proactive stance on repair planning. The goal is to minimize the impact of turbine outages by preemptively identifying potential issues and orchestrating scheduled repairs. By leveraging data analysis and repair monitoring, anticipating the need for future maintenance interventions becomes more systematic, fostering a culture of preparedness that secures continuous and efficient turbine operation.
Frequently Asked Questions
What are the essential components of effective steam turbine maintenance planning?
At the core of effective steam turbine maintenance planning are detailed inspection and outage planning, adherence to a comprehensive maintenance schedule, and collaboration with engineers to develop a customized strategy. It’s also essential to consider reliability, operational efficiency, and service quality during the planning stage.
How often should steam turbine maintenance be conducted?
The frequency of steam turbine maintenance can vary depending on the manufacturer’s recommendations, the turbine’s usage, and its operational context. Regular inspections are typically recommended, with comprehensive maintenance scheduled at strategic intervals to ensure efficiency, reliability, and safe operation.
Why is regular inspection and maintenance of steam turbines important?
Regular inspections and maintenance of steam turbines are vital for monitoring the condition of the equipment, identifying potential problems, and implementing proactive measures to reduce failure downtime. They help extend the life of the equipment by addressing wear and aging processes before they lead to failure.
How can proactive maintenance measures impact a steam turbine’s operation?
Proactive maintenance measures can significantly improve the reliability and efficiency of steam turbines. By identifying and rectifying issues before they escalate, these measures help prevent forced outages, reduce operational costs, and increase the overall longevity and profitability of the plant.
What is involved in developing a customized steam turbine maintenance plan?
Developing a customized steam turbine maintenance plan involves collaborating with experienced engineers to analyze the specific needs of the plant, pre-ordering necessary parts, optimizing outage times, considering potential equipment modernization, and setting strategies for reliable plant operation.
How critical is vendor selection when planning steam turbine maintenance?
Vendor selection is a crucial step in steam turbine maintenance planning. It involves evaluating the vendor’s machine capability, quality control, and technical expertise. Quality assurance is imperative, and a comprehensive vetting process ensures that the selected vendor meets the necessary standards for a successful maintenance outcome.
What strategies can be used to minimize downtime during steam turbine repairs?
To minimize downtime during repairs, strategies include timing and scheduling repairs to coincide with strategic operational periods, using remote monitoring and diagnostic tools to proactively manage risks, and having a detailed maintenance plan that includes efficient repair identification and scheduling.