The functionality and efficiency of industrial turbines are pillars of modern energy production. Understanding the intricate details behind the causes of industrial turbine malfunctions is crucial for maintaining consistent and reliable energy outputs.
Allied Power Group, standing at the forefront as the premier non-OEM provider of turbine repairs, insists on the importance of investigating and pinpointing the diverse factors that can lead to turbine breakdowns. Identifying the root of these issues is not only instrumental for immediate troubleshooting but also for formulating steadfast preventive measures.
In-depth failure analysis and a meticulous understanding of turbine breakdown factors are indispensable for energy companies to evade unscheduled downtimes and extensive repair costs.
Troubleshooting industrial turbine issues entail a complex amalgamation of technical know-how and applied experience in dealing with the intricate system components of these power-generating giants.
The consequences of overlooking these malfunctions could lead to decreased operational efficiency and, at worst, catastrophic failures. Recognizing the various industrial turbine malfunction causes stands as a testament to operational excellence and long-term sustainability in power generation.
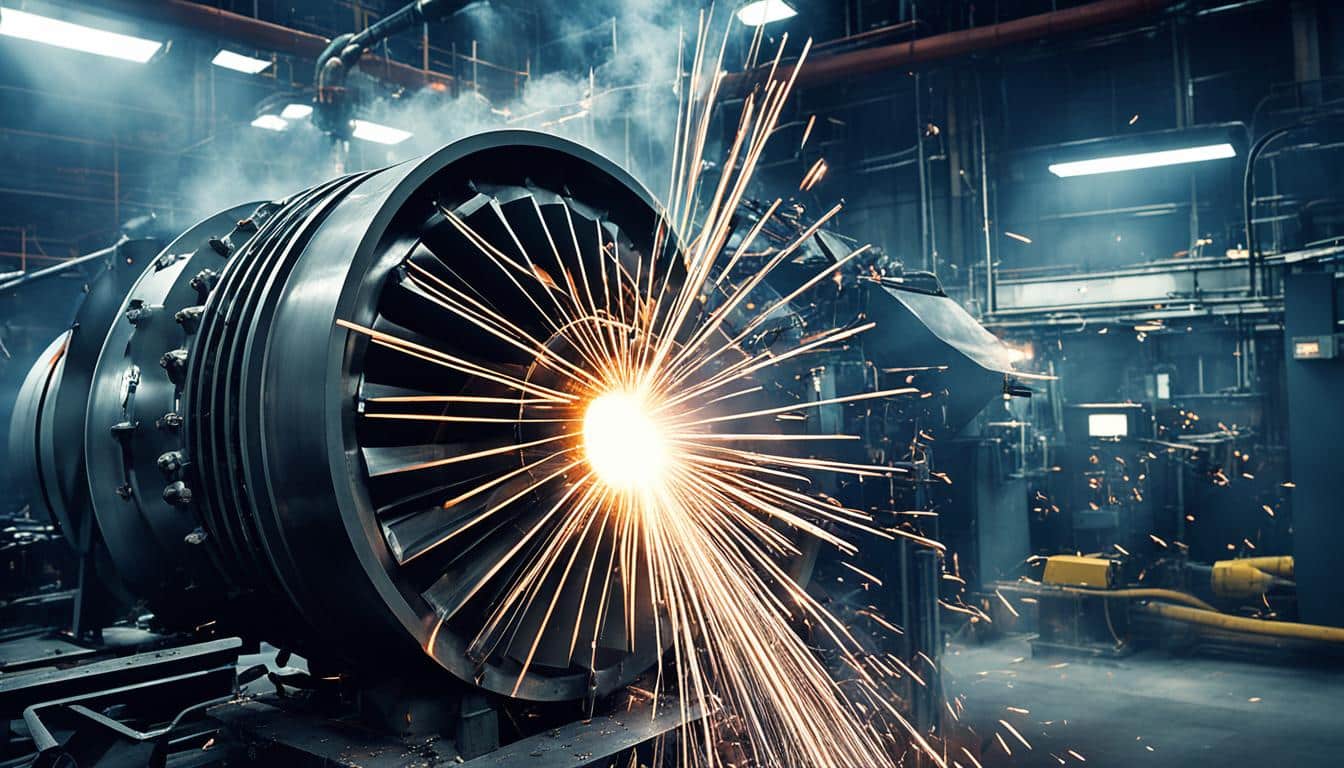
Key Takeaways
- Grasp the significance of diagnosing industrial turbine malfunction causes to ensure energy reliability.
- Recognize the imperative for detailed failure analysis to thwart future operational inefficiencies.
- Identify common factors contributing to turbine breakdowns and the urgency of troubleshooting.
- Acknowledge preventive measures as essential to safeguard against energy production disruptions.
- Understand the financial and operational implications of industrial turbine issues on the energy sector.
Understanding Gas Turbines
Gas turbines are a critical component in the modern energy landscape, transforming natural gas into mechanical energy and subsequently into electricity. Understanding the inner workings, functionality, and variety of gas turbines is essential for those in the energy and manufacturing sectors to grasp the challenges and intricacies of these powerful engines.
Basics of Gas Turbine Function
The operation of a gas turbine is built on the principle of extracting energy from high-temperature, high-pressure gas produced in a combustion chamber.
Air is compressed in the compressor section and then mixed with fuel, usually natural gas or aviation fuel, and ignited. The resulting hot gases expand rapidly and are directed over the turbine blades, causing the turbine blade to rotate and drive the compressor and the generator.
This process is known as the Brayton cycle, a constant-pressure thermodynamic cycle that is the foundation of gas turbine operation.
Key Components of a Gas Turbine
Within a gas turbine engine, several key turbine components work in synergy to convert fuel to power. The main elements include the compressor, combustion system, turbine, and exhaust.
The compressor draws in and compresses air, which is then heated up in the combustion chamber. Here, fuel injectors play a crucial role in spraying fuel into the combustion system. One of the most critical and intricate parts is the turbine blade, engineered to withstand extreme temperatures and stresses.
Other components like bearings and sealing systems ensure the machine operates smoothly and efficiently.
Types of Industrial Gas Turbines
Industrial gas turbines come in various types, each designed for specific applications and power generation needs. An understanding of these types helps in selecting the right turbine for the right application, ultimately impacting the performance and longevity of the turbine.
Type | Application | Characteristics | Compressor Type |
---|---|---|---|
Aero-derivative | Peak load power generation | Lightweight, rapid start-up | Axial flow |
Heavy-duty | Baseload power generation | Robust, high endurance | Centrifugal or axial flow |
Industrial | Mechanical drive applications | Customizable to application | Axial flow |
Each type is designed to operate under different circumstances, such as the lightweight aero-derivative for quick, responsive power generation and the sturdy heavy-duty turbines for continuous, high-demand energy production. Turbine Bearings, blade configurations, and sealing systems can vary between these types, affecting turbine efficiency and the need for maintenance.
Cross-Cutting Causes
When analyzing the integrity of industrial turbines, experts identify a spectrum of universal factors that impede performance and reliability. From the unavoidable deterioration over time to the missteps in maintenance routines, these issues transcend the branding or model of the equipment. This section peels back the layers on these common causes and their impact on turbine functionality.
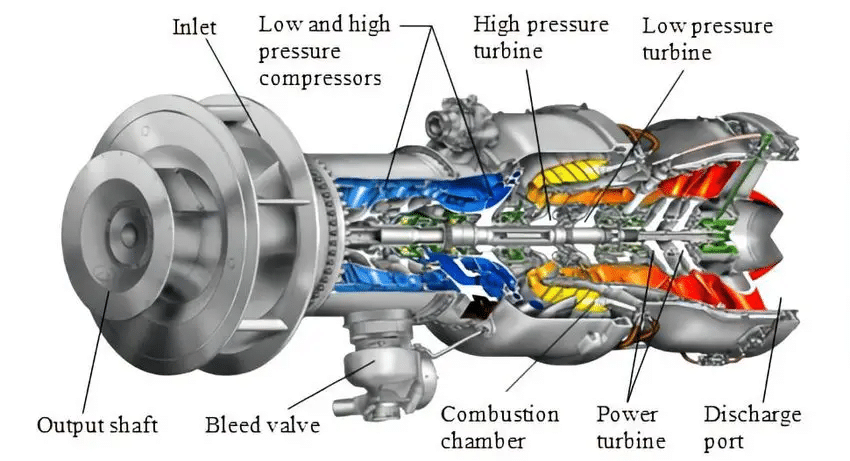
Wear and Tear
Turbine performance problems and turbine failure often originate from the natural wear and tear that components endure through regular use. Over time, the high-speed motion and constant pressure can lead to blade erosion, oxidation, seal degradation, and bearing fatigue — anomalies that gradually contribute to diminished efficiency and eventual component failure.
Improper Maintenance
Preventative turbine maintenance is not just a requisite; it’s the cornerstone of prolonging turbine life and preserving optimal performance and efficiency. Neglect in this area can lead to accelerated performance deterioration and unforeseen breakdown, underscoring the unavoidable connection between maintenance discipline and turbine longevity.
Operational Misuse
In addition to wear and physical maintenance, human factors in the form of turbine operating errors present noteworthy risks. Running turbines beyond designed parameters — be it load, temperature, or speed — can precipitate untimely malfunctions and expensive downtimes, flagging the need for stringent operational protocols.
Issue | Impact on Turbine Performance | Preventative Strategies |
---|---|---|
Blade Erosion | Loss of efficiency, imbalanced rotation | Regular inspections, material upgrades |
Seal Degradation | Pressure loss, increased leakage | Scheduled seal replacements, improved designs |
Bearing Fatigue | Overheating, increased vibration | Timely lubrication, load management |
Operating Errors | Premature failures, safety risks | Operator training, compliance with operation manuals |
Where Malfunctions Originate
The intricate design of industrial turbines allows for seamless energy production, yet the complex interplay of its high-performance components can be a breeding ground for malfunctions if not meticulously maintained.
In exploring the origins of such breakdowns, particular attention must be paid to the compressor, combustor, and the turbine blades themselves—all critical to the operational integrity of the system.
Compressor Complications
A turbine compressor has the chief responsibility is to manage the flow and pressure of air required for the combustion process. However, when inefficiencies arise, often due to blade damage or obstructions, the result is a chain reaction of thermal stress and a cascade of potential malfunctions throughout the turbine via unintended operating temperatures. A well-regulated cooling system is crucial to mitigate these risks and preserve compressor functionality under taxing operational demands.
Combustor Complications
The combustor, though robust by design to withstand the high temperatures and pressures of combustion, is not impervious to damage. Degradation often occurs from prolonged exposure to extreme conditions leading to combustor complications. Preservation of these components hinges upon an intricate balance of temperature and thermal stress management—a task that demands regular monitoring and proactive maintenance strategies.
Blade Fatigue and Cooling System Failures
Blade damage, whether by natural wear or foreign object impact, poses a critical risk to turbine efficiency. The extreme stress encountered by these blades can result in fatigue, necessitating advancements in the cooling system technology to extend their life span.
Cooling system failures not only accelerate blade degradation but also elevate the risk of high-temperature corrosion, further impairing the turbine’s reliability and performance.
How Fuel Quality Influences Performance
The integrity of turbine function is not solely dependent on mechanical parts, but is also significantly influenced by the quality of fuel it consumes. This section will examine the critical impacts of fuel quality on turbine performance, taking into account aspects such as fuel consumption, fuel quality, gas path health, temperature distribution, and contamination risks.
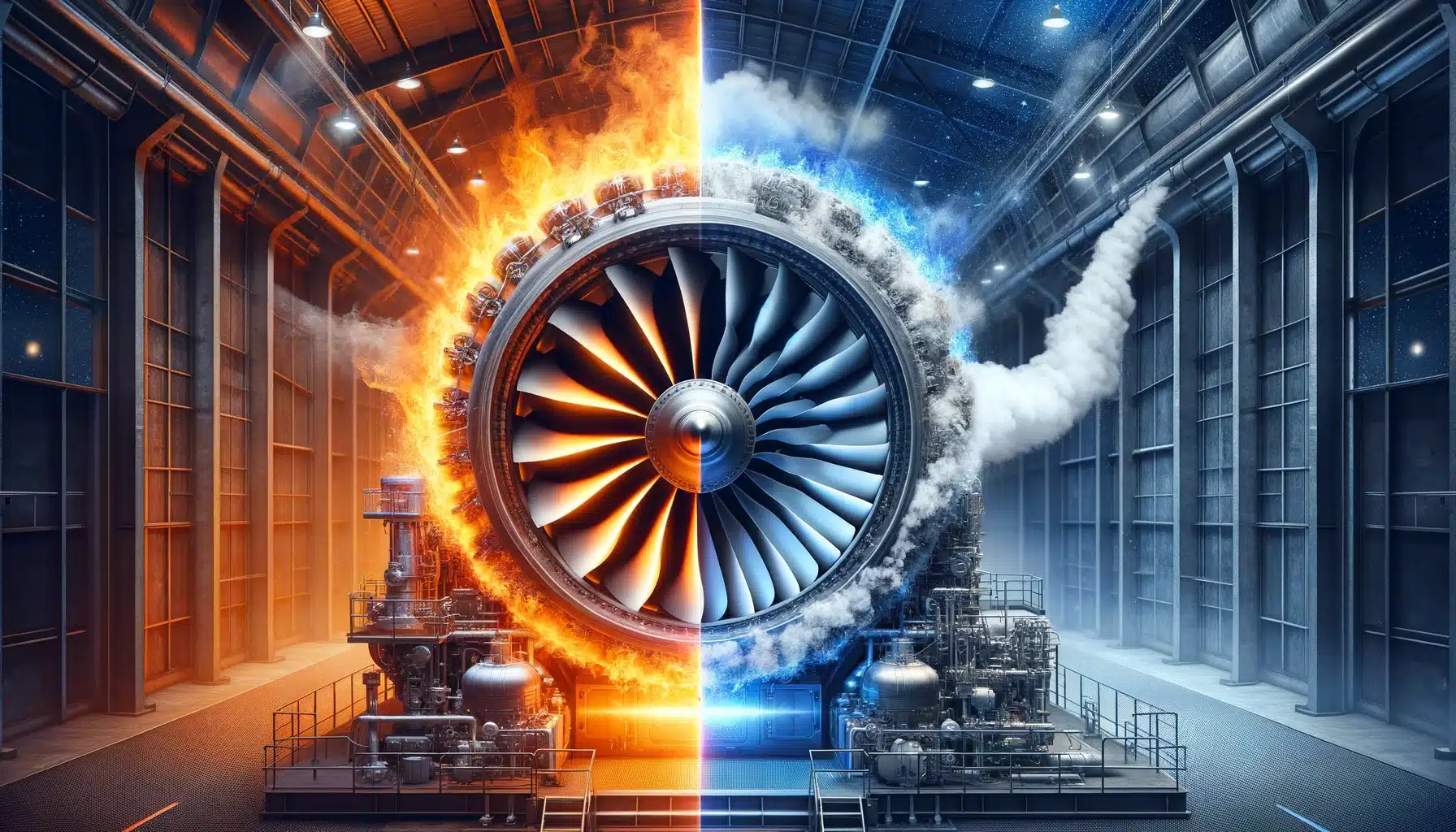
Fuel Impurities
Inferior fuel quality, laden with impurities like sulfur and vanadium, can lead to devastating turbine outcomes such as hot corrosion, which aggressively wears away turbine components. The presence of these contaminants can cause substantial blockages in the hot gas path, choking the turbine’s inlet air breath and hampering efficiency. Fuel contamination is a silent predator, resulting in unexpected downtime and costly repairs.
Fuel Type Variability
Fuel type variability plays a pivotal role in the operational stability of turbines. Differences in the chemical composition of fuel sources affect combustion processes, impacting temperature distribution across the turbine’s body. The use of inconsistent fuel types can lead to irregular thermal patterns, stressing turbine materials and potentially shortening their lifespan. It can even lead to complete gas turbine failure.
The Importance of Fuel Treatment
Implementing robust fuel treatment systems is not an option but a necessity for maintaining peak performance in turbines. These systems are pivotal in mitigating contamination risks and ensuring fuel quality is maintained at a level that promotes efficient consumption and optimal temperature distribution within the gas path. The table below illustrates the comparative effects of treated versus untreated fuel on turbine performance metrics.
Performance Metric | Untreated Fuel | Treated Fuel |
---|---|---|
Fuel Consumption Rate | Increased | Optimized |
Temperature Distribution | Irregular | Even |
Gas Path Cleanliness | Contaminated with Deposits | Reduced Contamination |
Maintenance Frequency | High | Reduced |
Risk of Corrosion and Wear | Increased | Minimized |
Environmental and External Malfunction Causes
Turbine reliability is greatly influenced by the environment in which they operate. Various external factors can severely impact their performance, sometimes leading to unexpected and costly malfunctions. Understanding these environmental causes is key to mitigating risks and maintaining the integrity of industrial turbines, particularly those powered by natural gas.
Ingestion of Foreign Objects
Ingestion occurs when foreign objects are drawn into turbines, potentially causing immediate and significant damage. These objects range from small particles to wildlife, each with varying implications on turbine components. To combat this, intricate filtration systems have been designed to prevent the ingestion of foreign objects, thus ensuring sustained reliability.
Atmospheric Conditions
Atmospheric conditions such as temperature fluctuations, humidity, and pollution can alter the behavior of natural gas as it combusts, influencing the overall effectiveness of the turbine’s performance. Regular analysis of atmospheric data is essential for adjusting operational parameters to maintain optimal turbine health and avoid malfunctions.
Corrosive Environments
Corrosive environments pose significant risks to turbines, especially in locations with high salinity or industrial pollution. These conditions can accelerate wear and compromise structural integrity. Coatings and advanced materials are employed to shield critical components from such corrosive factors.
Environmental Factor | Impact on Turbine | Mitigation Strategies |
---|---|---|
Ingestion of Foreign Objects | Physical damage to blades and internals, reduced efficiency | Advanced filtration systems, regular inspections |
Atmospheric Conditions | Performance variability, increased stress on components | Atmospheric monitoring, operational adjustments |
Corrosive Environments | Accelerated degradation, potential component failure | Use of corrosion-resistant coatings, material upgrades |
Conclusion
Through a detailed examination of industrial turbine malfunction causes, two persistent adversaries have been identified: erosion and corrosion. These formidable forces often spell the downfall of even the most robust turbine systems. To combat these challenges, reliability and preventative turbine maintenance emerge as the twin pillars critical to the extension of a turbine’s operational life.
The implementation of thorough failure analysis is pivotal, providing insights that fuel the proactive identification and mitigation of potential issues before they escalate into costly repairs or catastrophic failures.
By understanding the root cause of issues, maintenance teams can devise targeted strategies that not only fix immediate problems but also equip turbines against future threats. To safeguard the integral function of these turbines, it is imperative to uphold a strict regimen of maintenance and when necessary, to initiate a comprehensive overhaul.
It remains the responsibility of industry veterans like Allied Power Group to lead the forefront in delivering solutions and services that ensure turbine systems operate at peak efficiency and with unwavering reliability.
The intersection of specialized knowledge, expert repair, and steadfast maintenance forms the foundation of a successful turbine operation. Adherence to these principles by professionals ensures that turbines continue to function as the beating hearts of the industrial sector, powering our world’s ever-growing demand for energy.
Frequently Asked Questions
What are the common causes of industrial turbine malfunctions?
Common causes of industrial turbine malfunctions include wear and tear, improper maintenance, operational misuse, compressor complications, combustor issues, blade fatigue, cooling system failures, fuel quality issues, environmental factors such as foreign object ingestion, adverse atmospheric conditions, and corrosive environments.
How do gas turbines work?
Gas turbines operate by drawing in air through a compressor, heating it up in a combustor where fuel is burned, and then expelling it through a turbine section to produce mechanical power that is converted into electricity. This process relies on the continuous conversion of fuel to energy at high temperatures.
What are the key components of a gas turbine?
Key components of a gas turbine engine include the turbine blades, bearings, compressor, combustor, sealing systems, rotor, and vanes. Each plays a crucial role in the turbine’s operation, affecting its performance and reliability.
Why is preventative turbine maintenance important?
Preventative maintenance is essential for ensuring the reliability and longevity of turbines. It helps prevent deterioration, allows for the early detection of issues such as blade damage or thermal stress, and minimizes the risk of catastrophic failures. Proper maintenance schedules can also improve efficiency and reduce fuel consumption.
What can lead to compressor and combustor complications in turbines?
Compressor complications often result from imbalances in pressure and temperature, blockage, or misalignment, which can lead to efficiency losses and potential shutdowns. Combustor complications can be caused by overheat conditions, deterioration within combustion chambers, and deposition that affects temperature distribution and can lead to premature failure.
How does the quality of fuel affect gas turbine performance?
The quality of fuel directly influences combustion efficiency, temperature distribution within the turbine, and the accumulation of deposits in the gas path. Impurities and variability in fuel types can lead to hot corrosion, blockages, and other forms of contamination that degrade performance and necessitate more frequent maintenance or overhauls.
What environmental factors can cause turbine malfunctions?
Environmental factors like ingestion of foreign objects can lead to blade damage or blockages, while adverse atmospheric conditions and corrosive environments can lead to accelerated wear of turbine components due to erosion and corrosion. These factors can significantly disrupt the normal operation of gas turbines and compromise their reliability.